Resources
technical specifications, installation guides and standards you will ever need
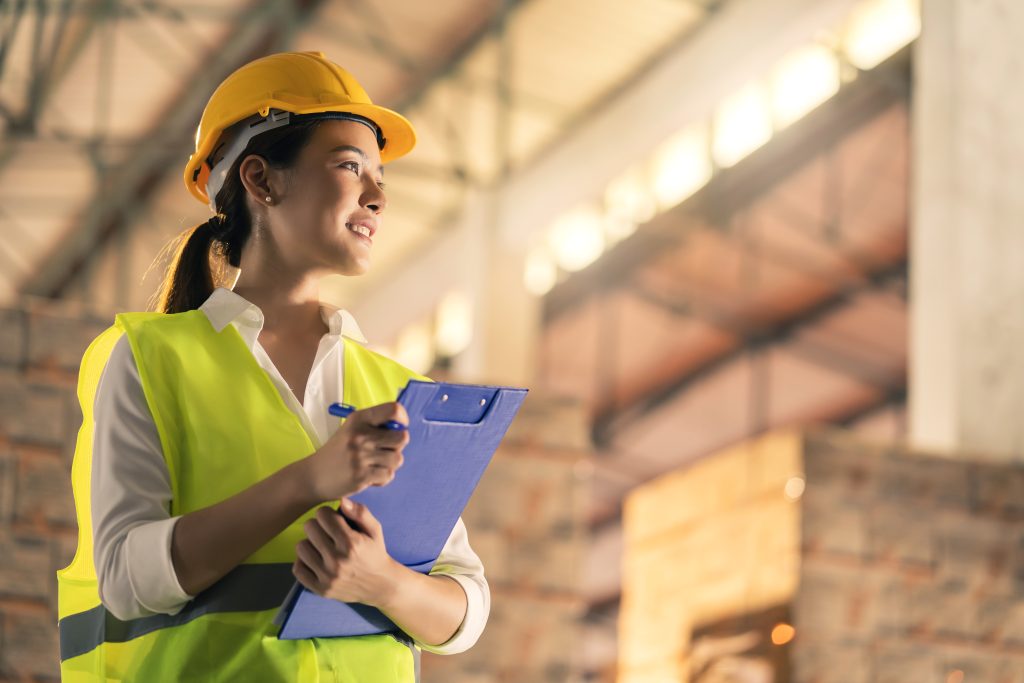
Technical specifications sheets
- RESPONSE TO YOUR NEEDS
- BUROBOX 19 - Wood core/Bottom tray - thickness 19 mm
- BUROBOX 30/38 - Resin bonded Core/bottom tray - thickness 30 ou 38 mm
- BUROBOX M0 - Mineral Core/bottom tray - thickness 30 mm
- GAMMABOX 30/38 - resin bonded core/Bottom tray + Covering
- GAMMAPAC 30/38 - High density resin bonded core/Bottom plate/ ABS surround/Covering
- GAMMAPAC MO - Mineral core / steel bottom plate / ABS surround / Covering
- MINIGAM - mineral core 18 mm / steel tray / top steel sheet
- ALUCAST - Monolithic aluminium panel plain or perforated
- PEDESTALS
- ACCESSORIES
Installation guides
Installation guides
Installation guides
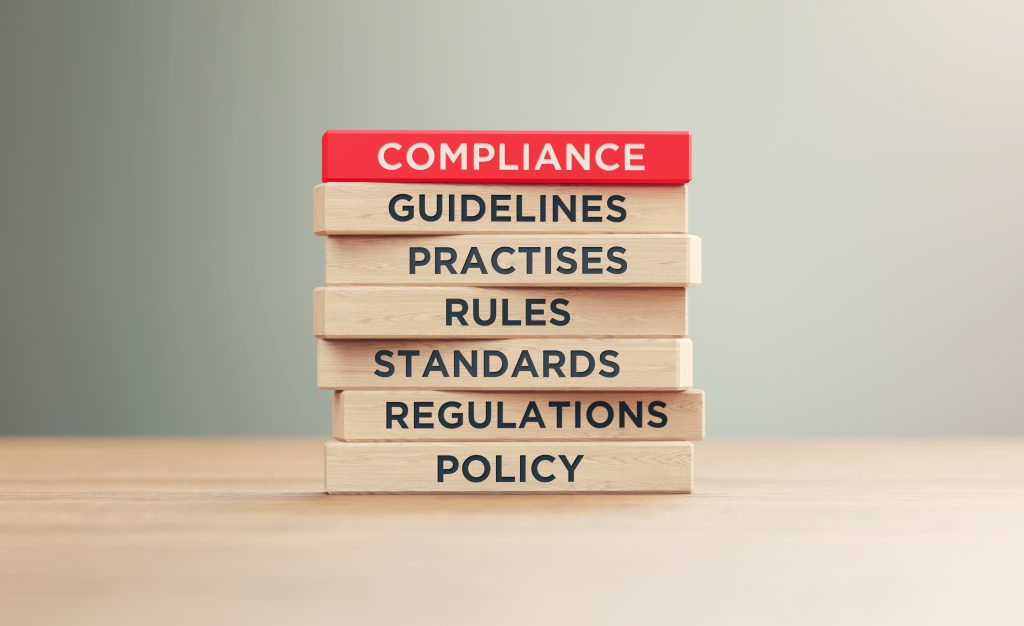
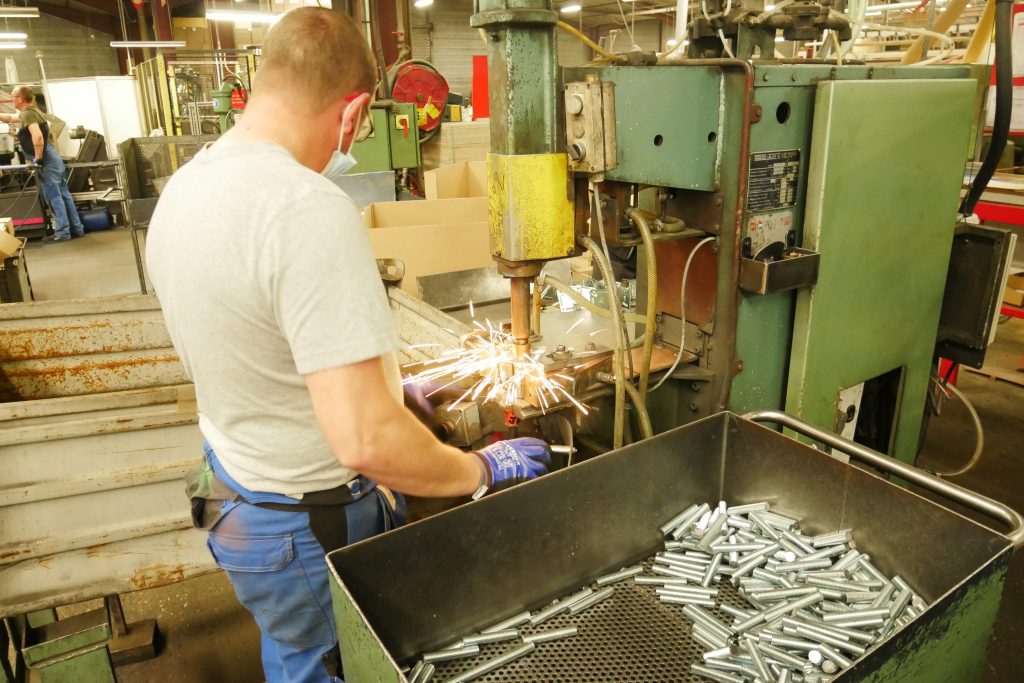
Standards (Summaries & Useful Links)
- EN 12825
- DTU 57.1.1
- Fire classification standards (M0, ML1, etc.)
- Wood standards EN 312 (excerpt)
- Electrical resistivity standards
- Acoustic insulation standards
- Terms of Sales
Frequently asked questions
Raised floors allow a space to be created between the raised floor and the original concrete floor. This void, known as a “plenum”, is used to accommodate all the utilities necessary for the proper functioning of a building: cables, air conditioning ducts, pipes, etc. The structure of the raised floor allows easy access to the plenum, whether for maintenance operations, alterations to these utilities, or the reorganisation of the existing space (change in the layout of partitions, etc.).
Chipboard is used for the most part thanks to its versatility, making it suitable for a wide range of uses.
Gamma Industries utilise des panneaux aggloméré de haute densité (680 à 720 kg/m3), de différentes épaisseurs, et de classe P6, pour usage intérieur et intensif. Ce bois aggloméré est issu à 100% de bois de recyclage.
Floor finish manufacturers offer a wide range of products, available in thousands of colours.
Our floors can be covered in laminate, PVC, carpet or hardwood finishes.
These finishes include imitation wood or concrete, can be pale or brightly coloured, feature distinct veining or varying degrees of decorative detail.
Contact us for any advice on the coatings of our products, the Gamma Industries teams will refer you to the supplier and its products most adapted to your needs.
For optimum precision when cutting, we recommend using band saws.
The usual method for removing panels consists in using a glass suction cup.
Some panels may require more sophisticated tools: double suction cups for heavy panels or clamping systems for those with carpeting.
Do not use screwdrivers or other tools with metal tips, as they may damage the panels.
Gamma Industries registered an EPD with INIES (the French national reference database for environmental and health data on construction products and equipment) under number 1-170:2021 (R1) in July 2021.
Placostil partitions can be used with our products. For safety purposes, it is advisable to install support pedestals parallel to the partition, depending on its weight.
The point load is the load applied at any point on the panel. You can refer to the documentation: “understand the NF EN 12825” In the standard, this load is applied by way of a 25×25 mm (+/-0.1 mm) cube, which represents the base of a piece of furniture.
This cube is then positioned with a given load at different points on the panel being tested. The deflection of the system is then measured until it breaks (“ultimate load”).
Generally, the panels are tested at a number of specific points:
- In the middle of one side of the panel
- In the centre of the panel
- At a point called Z, approximately 70 mm from the corner of the panel.
- At any point considered to be weak by the analysis laboratory.
The distributed load is defined as the total load that a raised access floor system can withstand.
This load, expressed in daN/m² (decanewtons per square metre), is approximately 5 times the point load tolerated by the panel at any point.
– under the class 1 system (working load of >200 daN, deflection of 2.5 mm and ultimate load of <400 daN), the maximum distributed load is approximately 5 x 200 = 1 t/m².
– under the class 4 system (working load of >450 daN, deflection of 2.5 mm and ultimate load of <900 daN), the maximum distributed load is approximately 5 x 450 = 2.25 t/m².
It all depends on the load that will be carried by the floor. The installation of stringers will provide the panels with additional support.
Each of our product technical specifications sheets includes the results of load tests carried out on installations with and without stringers (“freestanding” installations).
Stringers are U-shaped bars made of galvanised steel. Depending on the type of stringer, they can be snapped onto the pedestal heads by means of a locking nut, or secured in place using a screw. This system provides good stability and resistance to horizontal loads.
The depth of the stringer is adapted to the performance required:
- 30 mm deep: type 30/15
- 45 mm deep: type 45/15
In sections where raised flooring is installed over ducts, conduits, channels, etc., these stringers or profiles can be used to bridge such obstacles and eliminate the need for one or more pedestals. In these sections, a deflection of 20% more than that applied to the rest of the raised floor is allowed.
The base of the pedestals is glued to the floor using a specially designed adhesive, or by means of a mechanical device.
The base of each pedestal is fitted with a device (ridge) designed to attach the earthing strap quickly and securely.
Yes, it is imperative, to ensure that the electrostatic charge on the raised floor is eliminated.
All Gamma Industries pedestals meet the requirements of standard EN 12825: the maximum authorised load on a pedestal is at least equal to four times the maximum authorised load of the system being tested.
The recommended slope for ramps is 5%, with a maximum slope of 10%. The handling of loads on these ramps must be carried out using appropriate means under the responsibility of the user. A difference in slope between the nose of the ramp and the ramp itself is permitted.
Rigorous quality tests are carried out at every stage of the manufacturing process, in our factory analysis laboratory. We carry out destructive tests before and during manufacturing and on our finished products.
Many parameters are measured during production and in final control. They are subject to control records. This is one of the founding principles of ISO 9001.
The batches of Raw Materials are recorded to allow complete traceability of the production batches.
Yes, provided you use panels made from an inert material (e.g., mineral panels) such as BUROBOX M0, which can be finished with loose-lay carpet tiles.
The temperature that will be diffused underneath the panels is a key technical criterion when choosing a specific product. Other solutions may be considered depending on the requirements of the project.
In France, the fire resistance of raised access floors is defined by the Decree of 30 June 1983, amended by the Decree of 28 August 1991 and its appendices, which divide materials into five categories:
- M0 (incombustible)
- M1 (non-flammable),
- M2 (low flammability),
- M3 (moderately flammable),
- M4 (flammable).
Tests are carried out using radiation. The panel is tested on the plenum side (underside). On its upper side, the classification applicable is that of the finish.
A European standard has existed since 2016: EN 13501-2.
Partitioning of the plenum: where required by regulations, partitioning in incombustible (M0) materials can be supplied. The partitioned areas cannot exceed 300m².
We are particularly sensitive to environmental issues and have been implementing the following measures for several years:
- The identification and centralization of the technical and safety data sheets of all our suppliers.
- Development of environmental datasheets by product
- Improving the eco-design of our products, which has led to the use of chipboard panels made from 100% recycled wood. The factory producing these panels is itself powered by a biomass power plant
- Expanding the range of our products to include 100% HQE products
- Replacing all solvent-based products (e.g. vinyl glues and dust-proof paints)
- Focus groups on waste reduction, sorting, reuse and recycling of industrial waste and scrap
- Information of installation subcontractors
- Reducing and sorting installation waste, etc.
- Application of the French regulation on EPR (Extended Producer Responsibility) for construction projects and materials in the building sector since 1 May 2023.
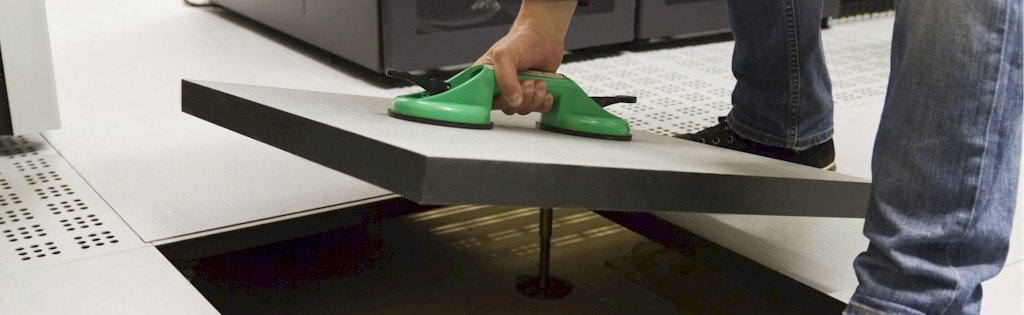